කිනිතුද්රව්ය කර්මාන්තයේ දී, එය පැතලි ඩයි පෙති මැෂින් හෝ මුද්දක් මිරා වල් පැලෑටි ද, ද්රව්යය අල්ලාගෙන අච්චුව කපන තලය මගින් අවශ්ය දිගට ඇතුළත් කරන්න.
අංශු මුද්රණ යන්ත්රය
පීඩන රෝලර් කවචයට ප්රධාන වශයෙන් විකේන්ද්රික පතුවළ, පෙරළීමේ ෙබයාරිංස් ඇතුළත් වේ, පීඩන රෝලර් පතුවළෙන් පිටත දරුණු ෂෙල් ස්ලයෙල්, සහ පීඩන රෝලර් කවචය සහාය දැක්වීම සහ සවි කිරීම සඳහා භාවිතා කරන සංරචක.
පීඩනය රෝලර්ෂෙල්ගේ අච්චු සිදුරට මිරිකීම මිරිකන අතර එය අච්චු කුහරය තුළ පීඩනයකට ලක් කරයි. පීඩන රෝලරය ග්රහණ බලය ලිස්සා යාම වැළැක්වීම සඳහා පීඩනය රෝලර් සහ ද්රව්ය අතර යම් iction ර්ෂණ බලයක් තිබිය යුතුය. එබැවින්, iction ර්ෂණය වැඩි කිරීම සහ ප්රතිරෝධය වැඩි කිරීමට පියවර බොහෝ විට පීඩන රෝලර් මතුපිටින් ගනු ලැබේ. පීඩන රෝලර් සහ අච්චුවේ ව්යුහාත්මක පරාමිතීන් තීරණය කරන විට, පීඩන රෝලරයේ පිටත පෘෂ් of යේ ව්යුහාත්මක ස්වරූපය සහ ප්රමාණය කැටිරු කාර්යක්ෂමතාව සහ අංශු ගුණාත්මක භාවයට සැලකිය යුතු බලපෑමක් ඇති කරයි.
පීඩන රෝලර් කවචයේ මතුපිට ව්යුහය
පවත්නා අංශු රෝලර් සඳහා පොදු වර්ග තුනක් මතුපිට තුනක් ඇත: අවුලුවන රෝලර් මතුපිට, අද්දර මුද්රා තැබීම සහ පැණි වදයේ රෝලර් මතුපිට.
දත් රූබයිඩ් වර්ගයේ පීඩන රෝලර්ට හොඳ රෝල් කිරීමේ කාර්ය සාධනයක් ඇති අතර පශු සම්පත් හා කුකුළු ආහාර කර්මාන්තශාලා වල බහුලව භාවිතා වේ. කෙසේ වෙතත්, දත් වලදී පෝෂණය ලිස්සා යාම නිසා, පීඩන රෝලර් සහ මුද්ද අච්චුවේ ඇඳුම ඉතා ඒකාකාරී නොවන අතර පීඩන රෝලර් සහ මුද්ද අච්චුව යන දෙකේම ඇඳුම වඩාත් දරුණු ය.
දාර මුද්රා තැබීම සමඟ දත් සහිත වලට් වර්ගයේ පීඩන රෝලර් ප්රධාන වශයෙන් ජලජ ද්රව්ය නිපදවීමට සුදුසු වේ. ජලජ ද්රව්ය නිස්සාරණය අතරතුර ලිස්සා යාමේ වැඩි අවදානමක් ඇත. දත් වලදී දත් වල අශ්වාරෝහක අශ්වාරෝහක මුද්රා තැබීම නිසා, පෝෂණ නිස්සාරණය අතරතුර දෙපැත්තටම ලිස්සා යාම පහසු නොවන අතර එහි ප්රති ing ලයක් ලෙස වඩාත් ඒකාකාරී ලෙස ආහාර බෙදා හැරීම. පීඩන රෝලර් ඇඳුමින් සැරසුණු අතර මුද්ද අච්චුව ද වඩාත් ඒකාකාර වන අතර එහි ප්රති ing ලයක් ලෙස නිපදවන ලද පෙති වල වඩාත් නිරන්තර දිගකි.
හනෙල්කොබ් රෝලර්ගේ වාසිය නම් රින්ග් අච්චුවේ ඇඳුම ඒකාකාරී වන අතර නිපුණතා අංශුවල දිග සාපේක්ෂව අනුකූල වේ. කෙසේ වෙතත්, දඟරයේ ක්රියාකාරිත්වය දුප්පත් වන අතර එය කැටිති වල ප්රතිදානයට බලපාන අතර තථ්ය නිෂ්පාදනයේ තථ්ය වර්ගය භාවිතා කිරීම තරම් පොදු නොවේ.
පහත දැක්වෙන්නේ බෝෂෙල් පීඩන රෝලර් මුද්ද අච්චු සඳහා අංශු මැෂින් පීඩන රෝලර් වර්ග 10 ක් වන අතර අවසාන 3 අනිවාර්යයෙන්ම ඔබ දැක නැති අයයි!
අංක 10 වලවල් වර්ගය
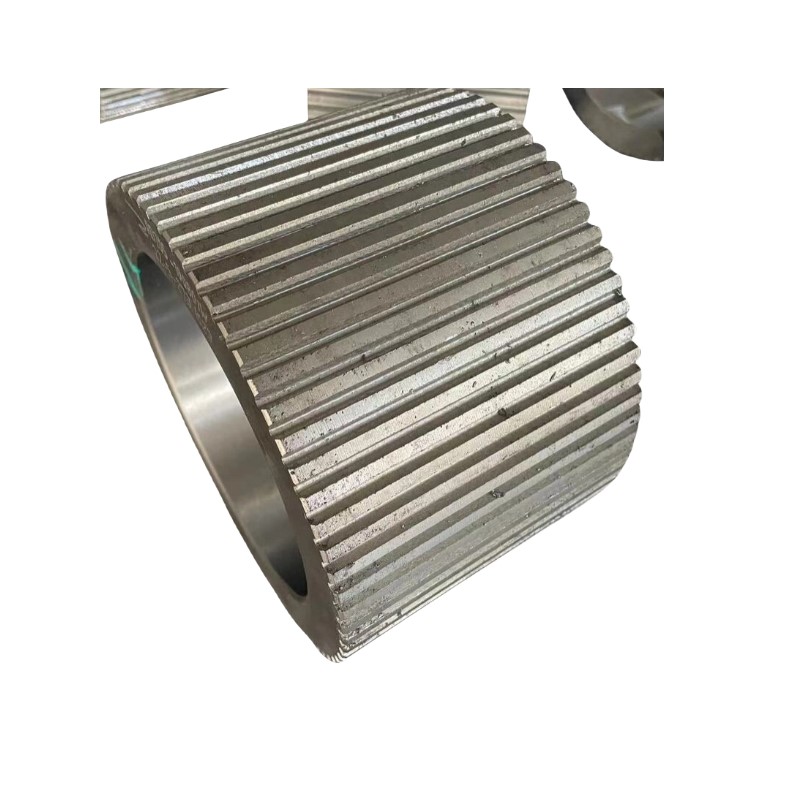
අංක 9 සංවෘත වලක් වර්ගය
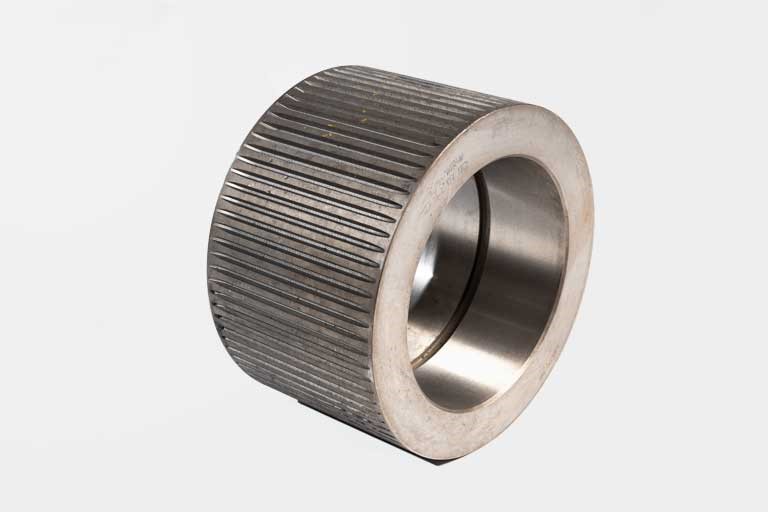
අංක 8 කුළුබඩු වර්ගය
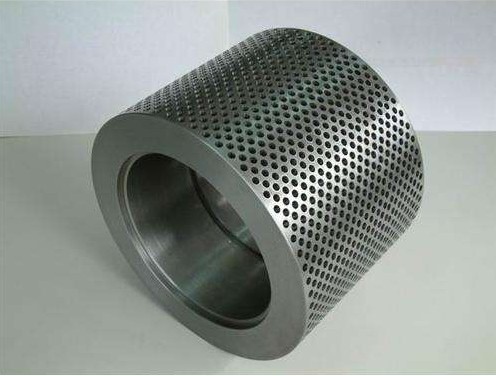
අංක 7 දියමන්ති හැඩැති
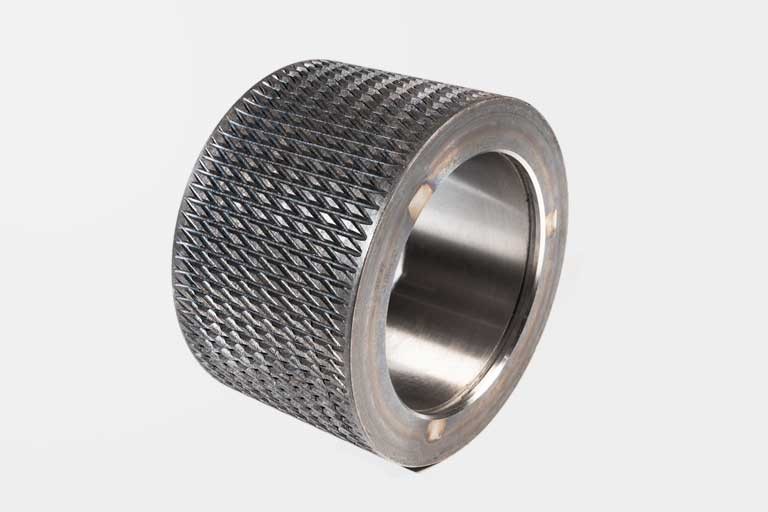
අංක 6 නැඹුරුවන වල
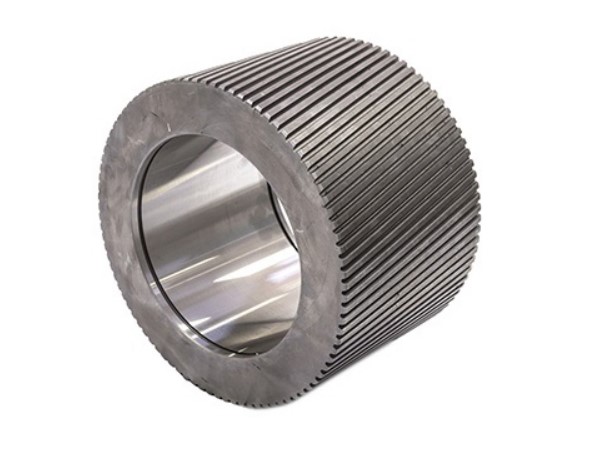
අංක 5 ග්රෝව් + පැණි වද
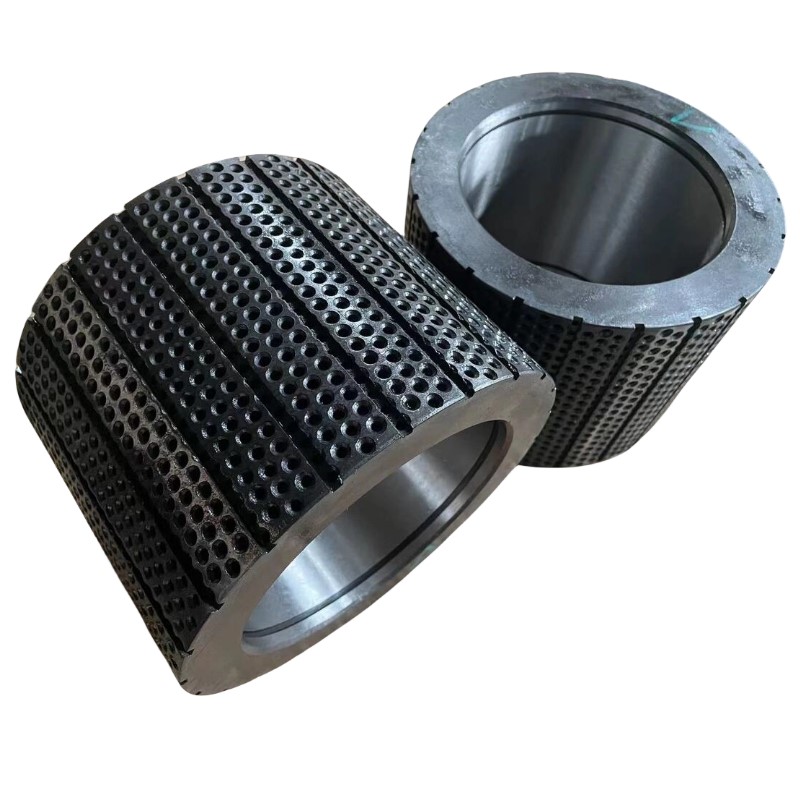
අංක 4 සංවෘත වලක් + පැණි වද
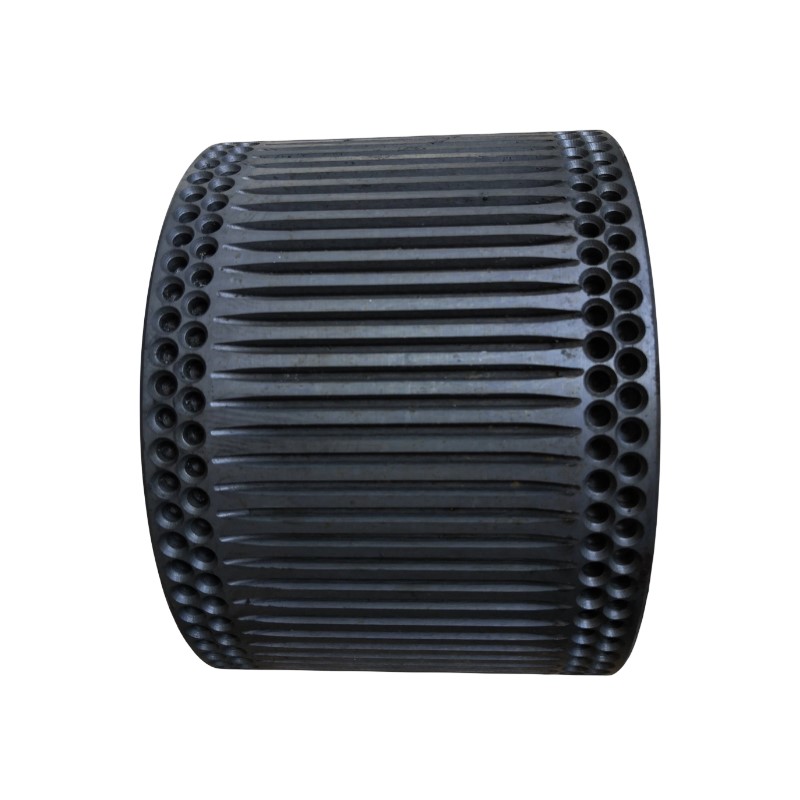
අංක 3 නැඹුරුවන ග්රෝව් + පැණි වද
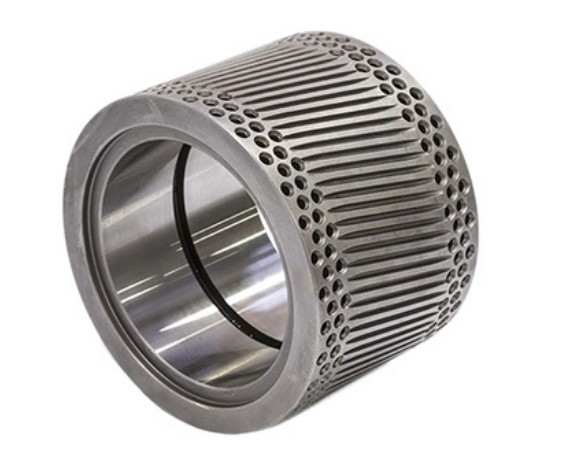
අංක 2 මාළු අස්ථි රැළි
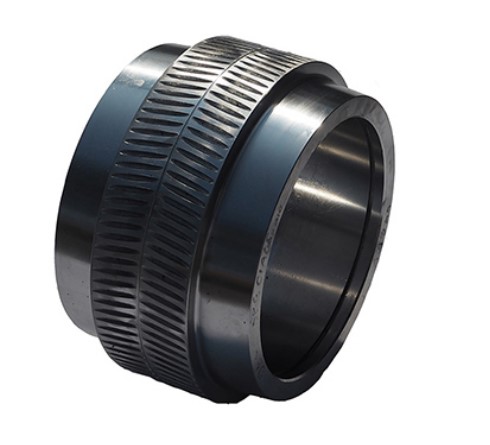
අංක 1 චාප හැඩැති රැළි
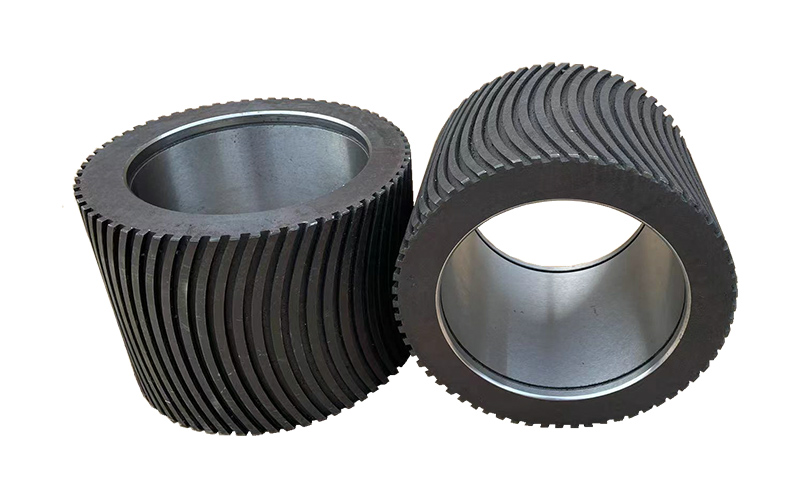
සෙප්පියාජික ආකෘතිය: ටංස්ටන් කාබයිඩ් කොලර් කවචය
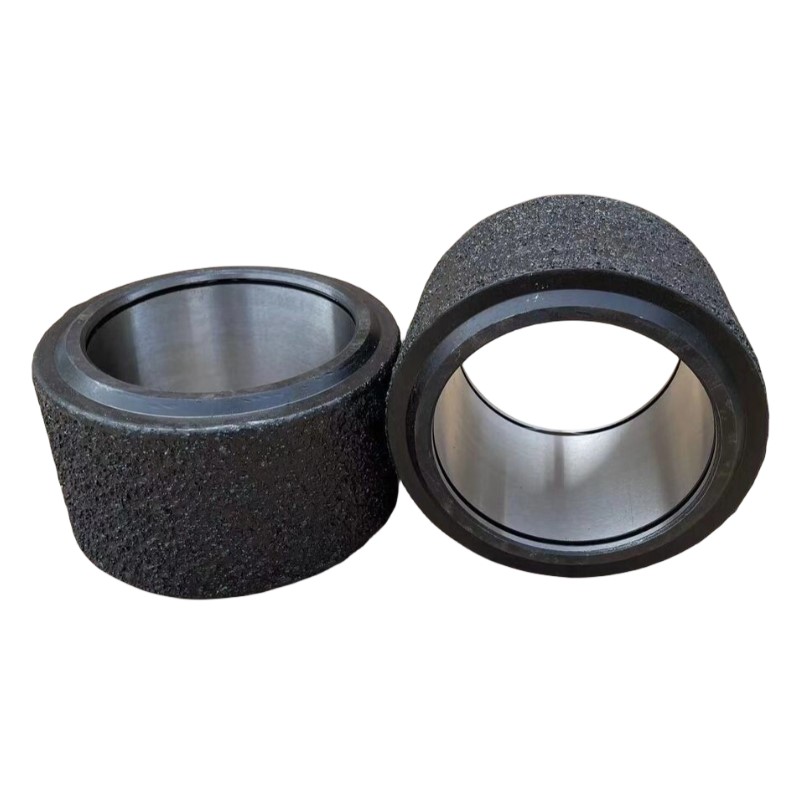
අංශු යන්ත්රයේ පීඩන රෝලර් ලිස්සා යාම සඳහා ප්රතිකාර ක්රමය
දරුණු වැඩ කරන පරිසරය නිසා, ඉහළ වැඩ කරන තීව්රතාව සහ පීඩන රෝලර් කවචයේ වේගවත් ඇඳුම් අනුපාතය, පීඩන රෝලර් අංශු යන්ත්රයේ අවදානමට ලක්විය හැකි වන අතර එය නිතිපතා ප්රතිස්ථාපනය කළ යුතුය. නිෂ්පාදන පුහුණුව නිෂ්පාදන ද්රව්යවල ලක්ෂණ වෙනස් වන තාක් කල්, සැකසුම් අතරතුර වෙනත් තත්වයන් වෙනස් වන තාක් කල්, අංශු යන්ත්රයේ පීඩන රෝලර් ලිස්සා යාමේ සංසිද්ධිය සිදුවිය හැකිය. කැටි ගැසීමේ ක්රියාවලියේදී පීඩන රෝලර් ලිස්සා යාමක් තිබේ නම්, කරුණාකර කලබල නොවන්න. නිශ්චිත විස්තර සඳහා කරුණාකර පහත සඳහන් ක්රමවේදයන් වෙත යොමු වන්න:
හේතුව 1: පීඩන රෝලර් සහ ස්පින්ඩල් ස්ථාපනය පිළිබඳ දුර්වල සංකීතභාවය
විසඳුම:
පීඩන රෝලර් කවචය එක් පැත්තකට මාරුවීම වළක්වා ගැනීම සඳහා පීඩන රෝලර් ෙබයාරිං ස්ථාපනය කිරීම සාධාරණ දැයි පරීක්ෂා කරන්න.
හේතුව 2: මුද්ද අච්චුවේ සීනුව මුඛය බිම පැතලි වන අතර එය ද්රව්ය අනුභව නොකිරීමට අච්චුව ලබා දෙයි
විසඳුම:
කැටි ගැසීම්, සම්ප්රේෂණ රෝද සහ කැටිති මුදු වල ඇඳුම පරීක්ෂා කරන්න.
0.3mm නොඉක්මවන දෝෂයක් සහිත වළල්ලේ පුෂ් කොටුවේ සාචලනය වෙනස් කරන්න.
පීඩන රෝලර් අතර පරතරය අනුව සකස් කළ යුතුය: පීඩන රෝලර් වල වැඩ කරන මතුපිටින් අඩක් අච්චුව සමඟ වැඩ කරන අතර පරතරය ගැලපුම් රෝදය ද හොඳ සේවා තත්ත්වයක් ඇති වේ.
පීඩන රෝලර් ලිස්සා යන විට, අංශු මැෂින්ට දිගු කලක් තිස්සේ තබා ගැනීමට ඉඩ නොදෙන්න.
නාද මංශීය විවරයෙහි සම්පීඩන අනුපාතය භාවිතා කරන ඉතා ඉහළ මට්ටමක පවතී, එය අච්චුවේ ඉහළ ද්රව්යමය විසර්ජන ප්රතිරෝධය ඇති කරන අතර පීඩන රෝලර් ලිස්සා යාමට එක් හේතුවක් ද වේ.
ද්රව්යමය පෝෂණයකින් තොරව පෙති යන්ත්රයට අනවශ්ය ලෙස නිෂ්ක්රීයව ඉඩ නොදිය යුතුය.
3 වන හේතුව: පීඩන රෝලර් දරණ හිර වී ඇත
විසඳුම:
පීඩන රෝලර් ෙබයාරිං වෙනුවට.
හේතුව 4: පීඩන රෝලර් කවචය වටකුරු නොවේ
විසඳුම:
රෝලර් කවචයේ ගුණාත්මකභාවය සුදුසුකම් නොලත්, රෝලර් කවචය ප්රතිස්ථාපනය කිරීම හෝ අලුත්වැඩියා කිරීම.
පීඩන රෝලර් ස්ලිප් කරන විට, පීඩන රෝලර් හි දීර් ilde icth ණත්වය වළක්වා ගැනීම සඳහා එය කාලෝචිත ආකාරයකින් නැවැත්විය යුතුය.
5 හේතුව: පීඩනය රෝලර් ස්පින්ඩල් නැමීම හෝ ලිහිල් කිරීම
විසඳුම:
ඩ්රින්යිල් වෙනුවට ආදේශ කරන්න හෝ තද කරන්න, සහ වළල්ලේ අච්චුව සහ පීඩන රෝලර් වෙනුවට පීඩන රෝලර් ස්පින්ඩල් හි තත්වය පරීක්ෂා කරන්න.
හේතුව 6: පීඩන රෝලර්ගේ වැඩ කරන මතුපිට මුද්ද අච්චුවේ වැඩ කරන මතුපිට සමඟ සාපේක්ෂව නොමඟ යවයි (දාරයේ හරස් මාර්ග)
විසඳුම:
පීඩන රෝලරය නුසුදුසු ලෙස ස්ථාපනය කර එය ප්රතිස්ථාපනය කරන්නේදැයි පරීක්ෂා කරන්න.
පීඩන රෝලර්ගේ විකාර පතුවළ විකෘති වී ඇත්දැයි පරීක්ෂා කරන්න.
ප්රධාන පතුවළ ෙබයාරිං හෝ අංශු යන්ත්රයේ බුෂිං හෝ බුෂිං මත ඇඳීම පරීක්ෂා කරන්න.
හේතුව 7: කැටිති කරකැවිල්ලේ ස්පින්ඩල් නිෂ්කාශනය කිරීම ඉතා විශාලය
විසඳුම:
කැටිකා පත්රයේ තද කිරීමේ නිෂ්කාශනය පරීක්ෂා කරන්න.
හේතුව 8: මුද්ද අච්චුවේ පන්ච් අනුපාතය අඩුයි (98% ට අඩු)
විසඳුම:
අච්චු සිදුර හරහා සරඹ කිරීම සඳහා පිස්තෝල සරඹයක් භාවිතා කරන්න, නැතහොත් එය තෙල්වල තම්බා ගන්න, පෝෂණය කිරීමට පෙර එය අඹරන්න.
හේතුව 9: අමුද්රව්ය ඉතා රළු වන අතර ඉහළ තෙතමනය ඇති අන්තර්ගතය ඇත
විසඳුම:
15% ක් පමණ තෙතමනය සහිත අන්තර්ගතයක් පවත්වාගෙන යාම කෙරෙහි අවධානය යොමු කරන්න. අමුද්රව්යවල තෙතමනය ප්රමාණය වැඩියි නම්, අමුද්රව්ය මුද්ද අච්චුවට ඇතුළු වූ පසු පුළු අවහිර කිරීම සහ ලිස්සා යාමක් ඇත. අමුද්රව්යවල තෙතමනය පාලනය කිරීමේ පරාසය 13-20% අතර වේ.
හේතුව 10: නව අච්චු පෝෂණය කිරීම වේගයෙන් පෝෂණය කිරීම
විසඳුම:
පීඩන රෝලර්ට ප්රමාණවත් කම්පනයක් ඇති බව සහතික කිරීම සඳහා වේගය සකසන්න, පීඩන රෝලර් ලිස්සා යාම වළක්වන අතර, වළල්ලේ අච්චුවේ ඇඳුම් සහ පීඩන රෝලර්ගේ ඇඳුම් වහාම පරීක්ෂා කරන්න.
පශ්චාත් කාලය: මාර්තු-25-2024