දුර්වල ජල ප්රතිරෝධය, අසමාන මතුපිට, ඉහළ කුඩු අන්තර්ගතය සහ අසමාන දිග?ජලජ ආහාර නිෂ්පාදනයේ පොදු ගැටළු සහ වැඩිදියුණු කිරීමේ පියවර
අපගේ දෛනික ජලජ ආහාර නිෂ්පාදනයේදී විවිධ පැතිවලින් අපට යම් යම් ගැටලුවලට මුහුණ දීමට සිදු වී ඇත.පහත දැක්වෙන පරිදි සෑම කෙනෙකු සමඟම සාකච්ඡා කිරීමට උදාහරණ කිහිපයක් මෙන්න:
1, සූත්රය
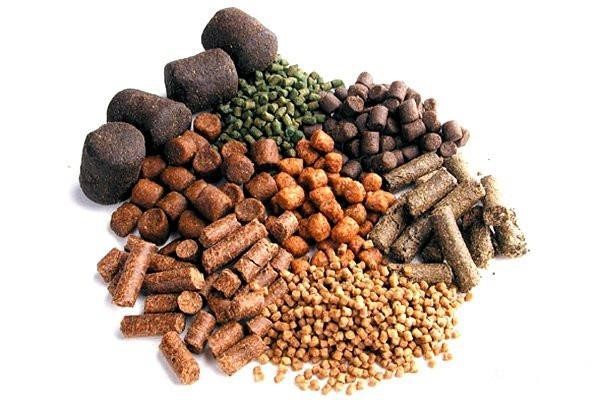
1. මත්ස්ය ආහාර සූත්ර ව්යුහය තුළ, අමු තන්තුවලට අයත්, රැප්සීඩ් කෑම, කපු ආහාර වැනි ආහාර අමුද්රව්ය වර්ග වැඩිය.සමහර තෙල් කම්හල්වල උසස් තාක්ෂණයක් ඇති අතර, තෙල් මූලික වශයෙන් ඉතා කුඩා අන්තර්ගතයක් සමඟ වියළි බදින ලද.එපමනක් නොව, මෙම වර්ගයේ අමු ද්රව්ය නිෂ්පාදනයේ දී පහසුවෙන් අවශෝෂණය නොවේ, එය කැටිති මත විශාල බලපෑමක් ඇති කරයි.මීට අමතරව, කපු කෑමක් තලා දැමීම දුෂ්කර වන අතර එය කාර්යක්ෂමතාවයට බලපායි.
2. විසඳුම: රැප්සීඩ් කේක් භාවිතය වැඩි කර ඇති අතර, සහල් නිවුඩ්ඩ වැනි උසස් තත්ත්වයේ දේශීය අමුද්රව්ය සූත්රයට එකතු කර ඇත.මීට අමතරව, සූත්රයේ දළ වශයෙන් 5-8% ක් පමණ වන තිරිඟු එකතු කර ඇත.ගැලපීම හරහා, 2009 දී කැටිති ආචරණය සාපේක්ෂව පරමාදර්ශී වන අතර, ටොන් එකක අස්වැන්න ද වැඩි වී ඇත.2.5mm අංශු ටොන් 8-9 අතර වන අතර එය අතීතයට සාපේක්ෂව ටොන් 2 කට ආසන්න වැඩිවීමකි.අංශුවල පෙනුම ද සැලකිය යුතු ලෙස වැඩිදියුණු වී ඇත.
මීට අමතරව, කපු ඇට කුඩු කිරීමේ කාර්යක්ෂමතාව වැඩි දියුණු කිරීම සඳහා, අපි තලා දැමීමට පෙර 2: 1 අනුපාතයට කපු ඇට සහ රැප්සීඩ් කෑම මිශ්ර කළා.වැඩිදියුණු කිරීමෙන් පසුව, තලා දැමීමේ වේගය මූලික වශයෙන් රැප්සීඩ් ආහාරයේ තලා දැමීමේ වේගයට සමාන විය.
2, අංශුවල අසමාන මතුපිට
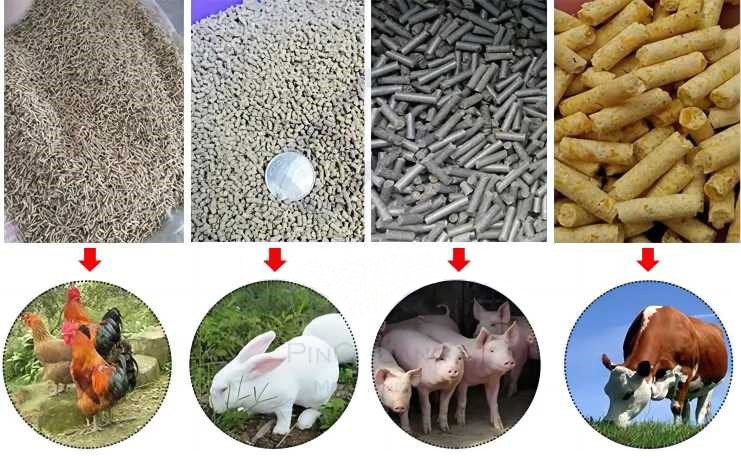
1. නිමි භාණ්ඩයේ පෙනුම කෙරෙහි විශාල බලපෑමක් ඇති අතර, ජලයට එකතු කරන විට, එය කඩා වැටීමට ලක් වන අතර අඩු උපයෝගිතා අනුපාතයක් ඇත.ප්රධාන හේතුව වන්නේ:
(1) අමුද්රව්ය ඉතා ගොරෝසු ලෙස තලා ඇති අතර, තෙම්පරාදු කිරීමේ ක්රියාවලියේදී ඒවා සම්පූර්ණයෙන්ම පරිණත වී මෘදු වී නොමැති අතර අච්චු සිදුරු හරහා ගමන් කරන විට අනෙකුත් අමුද්රව්ය සමඟ හොඳින් ඒකාබද්ධ කළ නොහැක.
(2) බොර තන්තු වල ඉහළ අන්තර්ගතයක් සහිත මාළු ආහාර සූත්රයේ, තෙම්පරාදු කිරීමේ ක්රියාවලියේදී අමුද්රව්යවල වාෂ්ප බුබුලු පැවතීම නිසා, අංශු සම්පීඩනයේදී අච්චුව ඇතුළත සහ පිටත අතර ඇති පීඩන වෙනස හේතුවෙන් මෙම බුබුලු කැඩී යයි. අංශුවල අසමාන මතුපිට ඇති කරයි.
2. හැසිරවීමේ පියවර:
(1) තලා දැමීමේ ක්රියාවලිය නිසි ලෙස පාලනය කරන්න
දැනට මත්ස්ය ආහාර නිෂ්පාදනයේදී අපේ සමාගම තොග අමුද්රව්ය ලෙස මිලිමීටර් 1.2 සිව් මයික්රෝ පවුඩර් භාවිතා කරයි.තලා දැමීමේ සියුම් බව සහතික කිරීම සඳහා අපි පෙරනයක් භාවිතා කිරීමේ වාර ගණන සහ මිටිය පැළඳීමේ මට්ටම පාලනය කරමු.
(2) වාෂ්ප පීඩනය පාලනය කරන්න
සූත්රයට අනුව, සාමාන්යයෙන් 0.2 පමණ පාලනය කරමින් නිෂ්පාදනයේදී වාෂ්ප පීඩනය සාධාරණ ලෙස සකස් කරන්න.මත්ස්ය ආහාර සූත්රයේ ඇති රළු කෙඳි අමුද්රව්ය විශාල ප්රමාණයක් නිසා උසස් තත්ත්වයේ වාෂ්ප සහ සාධාරණ තෙම්පරාදු කාලයක් අවශ්ය වේ.
3, අංශුවල දුර්වල ජල ප්රතිරෝධය
1. මෙම ආකාරයේ ගැටළුව අපගේ දෛනික නිෂ්පාදනයේ බහුලව දක්නට ලැබෙන අතර, සාමාන්යයෙන් පහත සඳහන් සාධක වලට සම්බන්ධ වේ:
(1) කෙටි තෙම්පරාදු කාලය සහ අඩු උෂ්ණත්වය නිසා අසමාන හෝ ප්රමාණවත් නොවන උෂ්ණත්වය, අඩු ඉදීමේ මට්ටම සහ ප්රමාණවත් තෙතමනය.
(2) පිෂ්ඨය වැනි අලවන ද්රව්ය ප්රමාණවත් නොවීම.
(3) මුද්ද අච්චුවේ සම්පීඩන අනුපාතය ඉතා අඩුය.
(4) සූත්රයේ ඇති තෙල් ප්රමාණය සහ බොර තන්තු අමුද්රව්යවල අනුපාතය ඉතා ඉහළ ය.
(5) අංශු ප්රමාණයේ සාධකය තලා දැමීම.
2. හැසිරවීමේ පියවර:
(1) වාෂ්ප තත්ත්වය වැඩි දියුණු කිරීම, නියාමකයේ තල කෝණය සකස් කිරීම, උෂ්ණත්වයේ කාලය දීර්ඝ කිරීම සහ අමුද්රව්යවල තෙතමනය නිසි ලෙස වැඩි කිරීම.
(2) සූත්රය සකසන්න, පිෂ්ඨය අමුද්රව්ය නිසි ලෙස වැඩි කරන්න, සහ මේදය හා අමු තන්තු අමුද්රව්යවල අනුපාතය අඩු කරන්න.
(3) අවශ්ය නම් මැලියම් එකතු කරන්න.(සෝඩියම් පදනම් වූ බෙන්ටොනයිට් පොහොරමය කොටස)
(4) හි සම්පීඩන අනුපාතය වැඩි දියුණු කිරීමමුද්ද මිය යයි
(5) හොඳින් තලා දැමීමේ සියුම් බව පාලනය කරන්න
4, අංශුවල අධික කුඩු අන්තර්ගතය
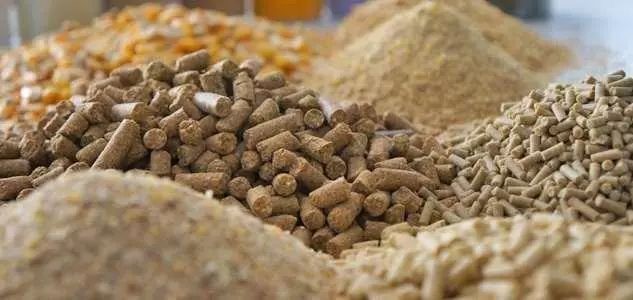
1. සිසිලනයෙන් පසුව සහ පිරික්සීමට පෙර සාමාන්ය පෙති පෝෂණයේ පෙනුම සහතික කිරීම අපහසුය.එම පෙතිවල සියුම් අළු සහ කුඩු වැඩි වශයෙන් තිබෙන බව පාරිභෝගිකයන් වාර්තා කර ඇත.ඉහත විශ්ලේෂණය මත පදනම්ව, මෙයට හේතු කිහිපයක් ඇතැයි මම සිතමි:
A. අංශු මතුපිට සුමට නැත, කැපීම පිළිවෙලට නැත, සහ අංශු ලිහිල් හා කුඩු නිෂ්පාදනයට නැඹුරු වේ;
B. ශ්රේණිගත කිරීමේ තිරය, අවහිර වූ තිර දැලක්, රබර් බෝල දැඩි ලෙස පැළඳීම, නොගැලපෙන තිර දැල් විවරය ආදිය මගින් අසම්පූර්ණ පරීක්ෂාව;
C. නිමි භාණ්ඩ ගබඩාවේ සියුම් අළු අපද්රව්ය විශාල ප්රමාණයක් ඇති අතර, නිෂ්කාශනය සම්පූර්ණ නොවේ;
D. ඇසුරුම් කිරීමේදී සහ කිරුම් කිරීමේදී දූවිලි ඉවත් කිරීමේදී සැඟවුණු අන්තරායන් ඇත;
හැසිරවීමේ පියවර:
A. සූත්ර ව්යුහය ප්රශස්ත කරන්න, මුදු මැරීම සාධාරණ ලෙස තෝරන්න, සහ සම්පීඩන අනුපාතය හොඳින් පාලනය කරන්න.
B. කැට සැකසීමේ ක්රියාවලියේදී, අමුද්රව්ය සම්පූර්ණයෙන්ම ඉදවීමට සහ මෘදු කිරීම සඳහා තෙම්පරාදු කිරීමේ කාලය, ආහාර ප්රමාණය සහ කැට උෂ්ණත්වය පාලනය කරන්න.
C. අංශු හරස්කඩ පිළිවෙලට ඇති බව සහතික කර වානේ තීරුවෙන් සාදන ලද මෘදු කැපුම් පිහියක් භාවිතා කරන්න.
D. ශ්රේණිගත කිරීමේ තිරය සකසන්න සහ නඩත්තු කරන්න, සහ සාධාරණ තිර වින්යාසයක් භාවිතා කරන්න.
E. නිමි භාණ්ඩ ගබඩාව යටතේ ද්විතියික පිරික්සුම් තාක්ෂණය භාවිතා කිරීම කුඩු අන්තර්ගත අනුපාතය බෙහෙවින් අඩු කළ හැකිය.
F. නිමි භාණ්ඩ ගබඩාව සහ පරිපථය නියමිත වේලාවට පිරිසිදු කිරීම අවශ්ය වේ.මීට අමතරව, ඇසුරුම්කරණය සහ දූවිලි ඉවත් කිරීමේ උපකරණය වැඩිදියුණු කිරීම අවශ්ය වේ.දූවිලි ඉවත් කිරීම සඳහා සෘණ පීඩනය භාවිතා කිරීම වඩාත් සුදුසුය, එය වඩාත් පරමාදර්ශී වේ.විශේෂයෙන්ම ඇසුරුම්කරණ ක්රියාවලියේදී ඇසුරුම් සේවකයා ඇසුරුම් පරිමාණයේ බෆර් ආප්පයෙන් දූවිලි නිතරම තට්ටු කර පිරිසිදු කළ යුතුය..
5, අංශු දිග වෙනස් වේ
1. දෛනික නිෂ්පාදනයේ දී, අපි බොහෝ විට පාලනය කිරීමේ දුෂ්කරතාවන්ට මුහුණ දෙමු, විශේෂයෙන් 420 ට වැඩි මාදිලි සඳහා. මේ සඳහා හේතු දළ වශයෙන් පහත පරිදි සාරාංශ කර ඇත:
(1) කැට සඳහා පෝෂණ ප්රමාණය අසමාන වන අතර, උෂ්ණත්වයේ බලපෑම විශාල වශයෙන් උච්චාවචනය වේ.
(2) අච්චු රෝලර් අතර නොගැලපෙන පරතරය හෝ මුද්ද අච්චුව සහ පීඩන රෝලර් දැඩි ලෙස පැළඳීම.
(3) මුදු අච්චුවේ අක්ෂීය දිශාව දිගේ, අන්ත දෙකෙහිම විසර්ජන වේගය මැදට වඩා අඩුය.
(4) මුද්ද අච්චුවේ පීඩනය අඩු කරන සිදුර ඉතා විශාල වන අතර, විවෘත කිරීමේ වේගය ඉතා ඉහළ ය.
(5) කැපුම් තලයෙහි පිහිටීම සහ කෝණය අසාධාරණ ය.
(6) කැටිති උෂ්ණත්වය.
(7) මුද්ද ඩයි කැපුම් තලයේ වර්ගය සහ ඵලදායී උස (තල පළල, පළල) බලපෑමක් ඇත.
(8) ඒ අතරම, සම්පීඩන කුටිය ඇතුළත අමුද්රව්ය බෙදා හැරීම අසමාන වේ.
2. ආහාර සහ පෙතිවල ගුණාත්මකභාවය සාමාන්යයෙන් විශ්ලේෂණය කරනු ලබන්නේ ඒවායේ අභ්යන්තර හා බාහිර ගුණාංග මත පදනම්වය.නිෂ්පාදන පද්ධතියක් ලෙස, අපි ආහාර පෙතිවල බාහිර ගුණාත්මක භාවයට සම්බන්ධ දේවල් වලට වැඩි වශයෙන් නිරාවරණය වේ.නිෂ්පාදන දෘෂ්ටිකෝණයකින්, ජලජ ආහාර පෙති වල ගුණාත්මක භාවයට බලපාන සාධක දළ වශයෙන් පහත පරිදි සාරාංශ කළ හැක:
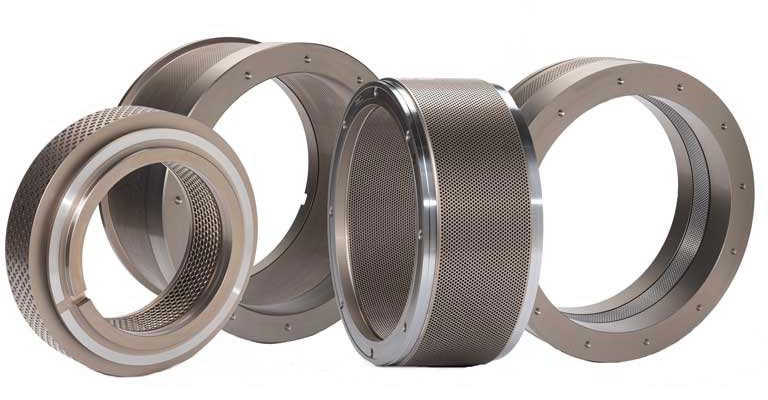
(1) සූත්ර සැලසුම් කිරීම සහ සංවිධානය කිරීම ජලජ ආහාර පෙතිවල ගුණාත්මක භාවයට සෘජු බලපෑමක් ඇති කරයි, එය මුළු එකතුවෙන් 40% ක් පමණ වේ;
(2) තලා දැමීමේ තීව්රතාවය සහ අංශු ප්රමාණයේ ඒකාකාරිත්වය;
(3) මුදු අච්චුවේ විෂ්කම්භය, සම්පීඩන අනුපාතය සහ රේඛීය ප්රවේගය අංශුවල දිග සහ විෂ්කම්භය කෙරෙහි බලපෑමක් ඇති කරයි;
(4) මුදු අච්චුවේ සම්පීඩන අනුපාතය, රේඛීය ප්රවේගය, නිවාදැමීමේ සහ තෙම්පරාදු කිරීමේ බලපෑම සහ අංශුවල දිග මත කැපුම් තලයේ බලපෑම;
(5) අමුද්රව්යවල තෙතමන අන්තර්ගතය, තෙම්පරාදු කිරීමේ බලපෑම, සිසිලනය සහ වියළීම නිමි භාණ්ඩවල තෙතමනය හා පෙනුම කෙරෙහි බලපෑමක් ඇති කරයි;
(6) උපකරණය, ක්රියාවලි සාධක, සහ නිවාදැමීමේ සහ තෙම්පරාදු කිරීමේ බලපෑම් අංශු කුඩු අන්තර්ගතයට බලපෑමක් ඇති කරයි;
3. හැසිරවීමේ පියවර:
(1) රෙදි සීරීමේ දිග, පළල සහ කෝණය සකස් කර, අඳින ලද සීරීම ප්රතිස්ථාපනය කරන්න.
(2) කුඩා පෝෂණ ප්රමාණය හේතුවෙන් නිෂ්පාදනයේ ආරම්භයේ දී සහ ආසන්නයේ දී කැපුම් තලයේ පිහිටීම නියමිත වේලාවට සකස් කිරීම කෙරෙහි අවධානය යොමු කරන්න.
(3) නිෂ්පාදන ක්රියාවලියේදී, ස්ථාවර පෝෂණ අනුපාතය සහ වාෂ්ප සැපයුම සහතික කරන්න.වාෂ්ප පීඩනය අඩු නම් සහ උෂ්ණත්වය ඉහළ යා නොහැකි නම්, එය නියමිත වේලාවට සකස් කිරීම හෝ නතර කළ යුතුය.
(4) අතර පරතරය සාධාරණ ලෙස සකස් කරන්නරෝලර් කවචය.නව රෝලර් සමඟ නව අච්චුව අනුගමනය කරන්න, සහ ඇඳීම හේතුවෙන් පීඩන රෝලරයේ සහ මුදු අච්චුවේ අසමාන මතුපිට ඉක්මනින් අලුත්වැඩියා කරන්න.
(5) මුද්ද අච්චුවේ මාර්ගෝපදේශ සිදුර අලුත්වැඩියා කර අවහිර වූ පුස් කුහරය වහා පිරිසිදු කරන්න.
(6) මුද්ද අච්චුව ඇණවුම් කිරීමේදී, මුල් මුද්ද අච්චුවේ අක්ෂීය දිශාවේ දෙපස ඇති සිදුරු පේළි තුනේ සම්පීඩන අනුපාතය මැදට වඩා 1-2mm කුඩා විය හැක.
(7) මුදු අච්චුව සහ පීඩන රෝලරය අතර දැල් රේඛාව මත ඇති පරිදි, හැකිතාක් තියුණු දාරයක් සහතික කිරීම සඳහා, 0.5-1mm අතර ඝනකමකින් යුත්, මෘදු කැපුම් පිහියක් භාවිතා කරන්න.
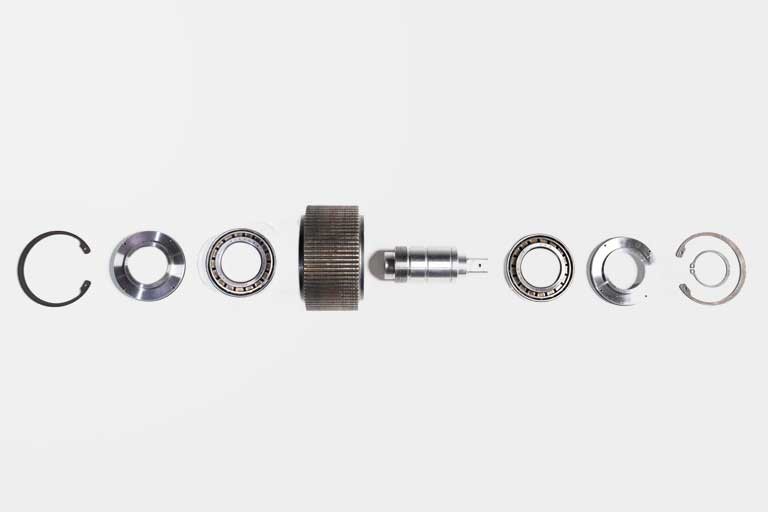
(8) මුද්ද අච්චුවේ සාන්ද්රණය සහතික කිරීම, කැටිතියේ ස්පින්ඩල් නිෂ්කාශනය නිතිපතා පරීක්ෂා කර අවශ්ය නම් එය සකස් කරන්න.
6, සාරාංශ පාලන ලක්ෂ්ය:
1. ඇඹරීම: පිරිවිතර අවශ්යතා අනුව ඇඹරීමේ සියුම් බව පාලනය කළ යුතුය
2. මිශ්ර කිරීම: සුදුසු මිශ්ර කිරීමේ ප්රමාණය, මිශ්ර කිරීමේ කාලය, තෙතමනය සහ උෂ්ණත්වය සහතික කිරීම සඳහා අමුද්රව්ය මිශ්ර කිරීමේ ඒකාකාරිත්වය පාලනය කළ යුතුය.
3. කල් පිරීම: පිපිරුම් යන්ත්රයේ පීඩනය, උෂ්ණත්වය සහ තෙතමනය පාලනය කළ යුතුය
අංශු ද්රව්යයේ ප්රමාණය සහ හැඩය: සම්පීඩන අච්චු සහ කැපුම් තලවල සුදුසු පිරිවිතරයන් තෝරා ගත යුතුය.
5. නිමි ආහාරවල ජල අන්තර්ගතය: වියළීම සහ සිසිලන කාලය සහ උෂ්ණත්වය සහතික කිරීම අවශ්ය වේ.
6. තෙල් ඉසීම: නිශ්චිත තෙල් ඉසීමේ ප්රමාණය, තුණ්ඩ ගණන සහ තෙල්වල ගුණාත්මකභාවය පාලනය කිරීම අවශ්ය වේ.
7. Screening: ද්රව්යයේ පිරිවිතරයන්ට අනුව පෙරනයේ ප්රමාණය තෝරන්න.
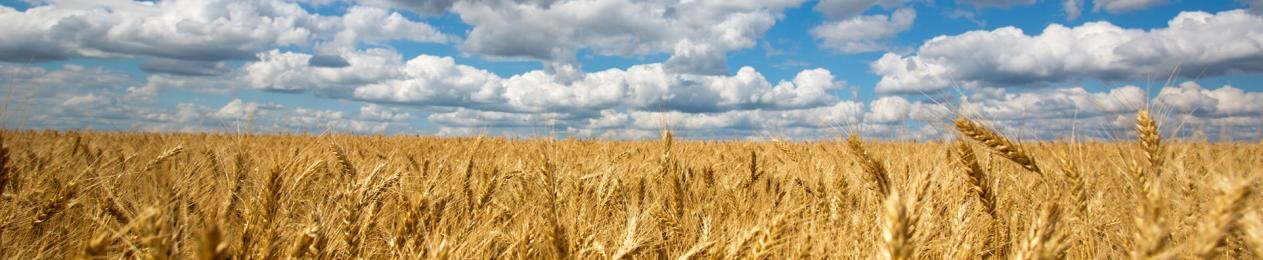
පසු කාලය: නොවැම්බර්-30-2023